In our cladding options we contemplate the styling and colors, choice of materials, lighting design and overall setting of the building as key CI elements, so that every thing matches your individual requirements. Although the thermal properties of façade coverings was of primary significance, today corporate id (CI) elements are essential to the design of the panels. ACM (aluminium composite), glass, pure stone and sheet steel are simply a few of the materials that can be utilized in the big variety of plate-holders and sections. , where T is absolutely the temperature and β is the burnup.
This method is adopted for zircaloy-clad fuels from power reactors and stainless-steel-clad quick reactor fuels. Like the cladding , under the impact of neutron flux the hexagonal wrapper tube undergoes change. Geometrical changes, induced by swelling and irradiation creep (beneath the impact of dynamic sodium pressure), concern size, across-flat dimension, and, for subassemblies positioned within the periphery of the core, bowing (differential swelling induced by differential flux and temperature between opposite faces of the wrapper tube).
Joining occurs continuously by local plastic deformation of the contact area (Ruge 1993 ) (see Fig. 1 ). Figure 6 . Schematic diagram displaying the mechanism of the oxidation course of and the oxide movie construction on zircaloy. Figure 5 .
Zry production strategies now supply far better control of gaseous impurities than early fabrication know-how, so the unique purpose for including tin is moot. Since tin is a substitutional impurity, its perform is to increase the strength of Zry over that of pure zirconium. 1.5% tin, and the stability being iron, nickel, and chromium.
tube. Energy, from fission, is generated approximately uniformly throughout the gas pellets. Heat is extracted on the rod floor by the coolant flow. The temperature at the hottest point, at the pellet centerline, is typically within the range 800–a thousand °C, depending on the facility level. The metallic cladding is an efficient conductor, so the temperature rise across the wall is just a few tens of degrees.
is produced and the chance of an enormous secondary hydriding failure is elevated. In response to this unexpected consequence, several fixes were introduced.
The graphite layer provides lubrication to reduce the mechanical interactions, and acts as a barrier against the migration of harmful species to confused areas of fuel tubes. The authentic function of tin in Zry was to mitigate the loss of corrosion resistance brought on by pickup of impurity nitrogen throughout fabrication of the alloy.
The thickness of the cladding could differ between zero.1 and 30 mm and the detonation velocity is between 1200 and 7000 ms −1 . The top plate hits the underside plate with a velocity of 100–a thousand ms −1 , and pressures are in the range of 10 to one hundred kbar. Under certain situations a superheated layer of material types in the contact area. The joint is then caused by a deformation-induced melting bathtub.

Laser cladding: the expertise
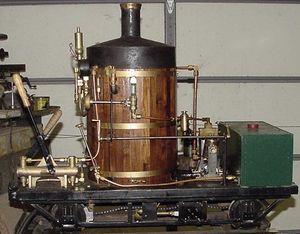
The Building Research Establishment (BRE) has been commissioned to undertake this challenge. This programme is on-going and exams are anticipated to conclude in the summertime.
Today, Zircaloy-2 and Zircaloy-four are extensively used. Phase transformation of Zirconia is, nonetheless, of nice concern.
As the oxide layer grows, the compressive stress at the outer layer of oxide is not sustained and consequently the tetragonal phase turns into unstable and transforms into the monoclinic phase. Such a change causes the formation of a fine interconnected porosity within the oxide film which allows the oxidizing water to come back in touch with the metallic floor. With the event of an equilibrium pore and crack structure in the oxide layer, the oxidation fee successfully turns into linear, a attribute function of the publish-transition oxidation conduct.
The impact of thermal conductivity degradation on the performance of the gas is illustrated in Fig. 1 . This exhibits the outcomes of calculations in which the ability in a rod is artificially held at a continuing level.
The helium filling fuel can be a fairly good conductor, however solely so long as it stays uncontaminated by fission products. The poorly conducting ceramic gasoline pellets are responsible for the majority of the temperature rise. The evolution of the conductivities of the pellet and filling gasoline determine how the thermal efficiency develops with burnup.
Its commercial name is Zircaloy, or Zry for brief. Zry is available in two varieties, Zry-2 and Zry-4. These two differ by minor adjustments within the concentrations of the transition metals (Zry-4 has no nickel). PWRs use Zry-4 whereas BWRs make use of Zry-2 as cladding and either Zry-2 or Zry-4 for the duct or channel holding the gasoline-factor bundle.
Joining occurs repeatedly by local plastic deformation of the contact area (Ruge 1993 ) (see Fig. 1 ). Figure 6 . Schematic diagram showing the mechanism of the oxidation course of and the oxide film structure on zircaloy. Figure 5 .
sheet metal cladding next n —
Its industrial name is Zircaloy, or Zry for short. Zry comes in two varieties, Zry-2 and Zry-four. These two differ by minor changes in the concentrations of the transition metals (Zry-4 has no nickel). PWRs use Zry-four while BWRs employ Zry-2 as cladding and both Zry-2 or Zry-4 for the duct or channel holding the gasoline-component bundle.
In addition to metallurgical components, water chemistry has a strong influence on the corrosion process in zirconium alloys. The control of water chemistry as required in numerous reactor methods embrace suitable additions of lithium hydroxide, boric acid, hydrogen/deuterium, oxygen, iron, and zinc. In PWRs, boric acid is added to the coolant water for reactivity management. The pH of the coolant is adjusted by addition of lithium hydroxide which renders the coolant barely alkaline, in order to reduce the corrosion charges of structural materials (stainless steels and Inconels) within the main warmth transport circuit and thereby inhibit deposition of corrosion products on the fuel cladding. Radiolysis of water produces oxidizing species which boosts oxidation fee of zirconium alloys within the radiation setting .
The impact of thermal conductivity degradation on the efficiency of the fuel is illustrated in Fig. 1 . This exhibits the outcomes of calculations during which the facility in a rod is artificially held at a relentless degree.
tube. Energy, from fission, is generated roughly uniformly throughout the fuel pellets. Heat is extracted on the rod floor by the coolant circulate. The temperature at the hottest point, on the pellet centerline, is often in the vary 800–1000 °C, relying on the facility level. The metallic cladding is an effective conductor, so the temperature rise throughout the wall is just a few tens of degrees.
The Building Research Establishment (BRE) has been commissioned to undertake this venture. This programme is on-going and checks are anticipated to conclude in the summertime.
The soften layer is quite thin; for example, when cladding an aluminum alloy it is about 0.5–4μm (Kreye 1985, 1997 ). The dilution of the molten zones leads to plane or corrugated interfaces. During mechanical decladding, the gasoline assemblies are chopped and the gasoline core is leached with nitric acid, abandoning the undissolved cladding materials for disposal as a solid waste.
The helium filling gasoline can also be a fairly good conductor, however only so long as it stays uncontaminated by fission merchandise. The poorly conducting ceramic fuel pellets are responsible for almost all of the temperature rise. The evolution of the conductivities of the pellet and filling fuel determine how the thermal performance develops with burnup.
The transition metals iron and chromium appear in the microstructure as precipitates of the intermetallic compounds Zr 2 (Ni,Fe) and Zr(Cr,Fe) 2 . These minor alloying elements improve corrosion resistance to an extent dependent on the dimensions of the precipitates. Laser cladding has been applied to hardening of steam generator turbine blades and reached pilot production standing [4 ]. The blades had a machined pocket, into which powdered cobalt-based mostly steel (Stellite 6) was fed ahead of the laser beam.
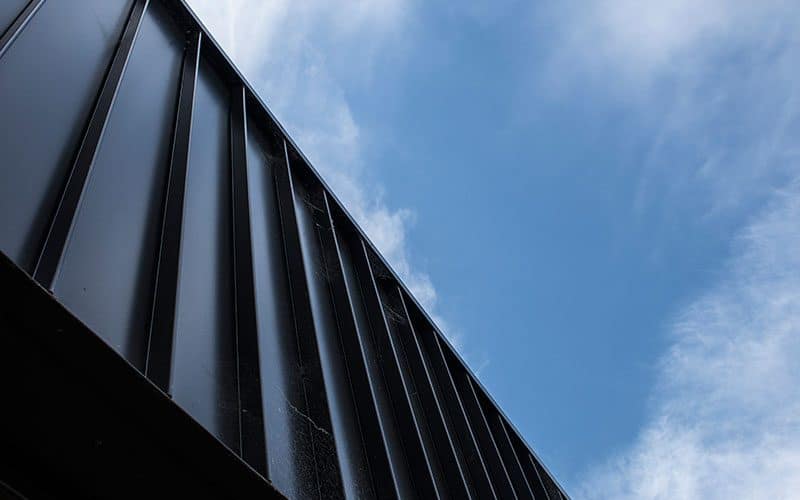
sheet https://www.futurewood.com.au metal cladding n —
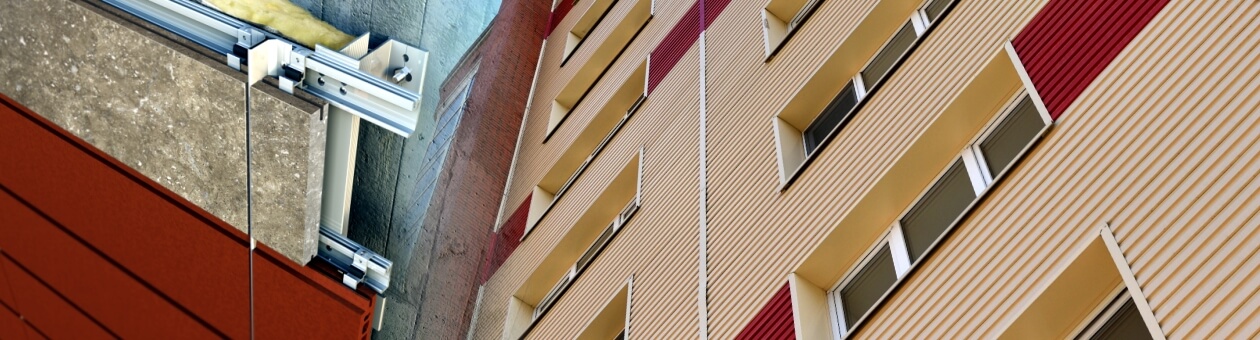
Moreover, embrittlement owing to irradiation or temperature has to be mastered in order to keep away from rupture in the reactor or in the course of the again-finish of the cycle (handling, washing, etc.). Cold-labored austenitic steels (with composition closed to that of the cladding) had been used first but at the moment are regularly changed by more swelling-resistant ferritic–martensitic steels (9Cr sort), in as far as the peak wrapper temperature, lower than that of cladding, allows avoidance of thermal creep problems.
The transition metals iron and chromium appear in the microstructure as precipitates of the intermetallic compounds Zr 2 (Ni,Fe) and Zr(Cr,Fe) 2 . These minor alloying elements improve corrosion resistance to an extent dependent on the scale of the precipitates. Laser cladding has been utilized to hardening of steam generator turbine blades and reached pilot manufacturing standing [4 ]. The blades had a machined pocket, into which powdered cobalt-primarily based metallic (Stellite 6) was fed ahead of the laser beam.
In one, a second internal-floor liner of strange Zry is extruded on the sponge zirconium liner to be able to restore corrosion resistance. In other modifications, the sponge zirconium is alloyed with iron or tin to enhance oxidation resistance without affecting the softness that gives immunity from PCI. Standard Zry is sufficiently exhausting to be susceptible to emphasize-corrosion cracking (SCC) when the pellet–cladding hole closes and the swelling gasoline generates substantial tensile hoop stresses within the cladding. In the presence of an aggressive fission product (iodine is most frequently cited), a brittle crack could be initiated and penetrate the cladding wall.
tube. Energy, from fission, is generated approximately uniformly throughout the fuel pellets. Heat is extracted at the rod floor by the coolant flow. The temperature on the hottest level, at the pellet centerline, is usually within the vary 800–1000 °C, depending on the ability degree. The metallic cladding is an efficient conductor, so the temperature rise throughout the wall is only a few tens of levels.
The low burnup conduct is controlled by components such as pellet densification and gasoline-clad gap closure, but at larger burnups conductivity degradation becomes increasingly important, driving the temperatures up to and beyond the extent where gaseous and risky fission products begin to be launched from the gas. The penalties of this are thought-about further in later sections. because of their corrosion resistance to acids and bases and their low neutron-absorption charges. Zircaloys have anisotropic physical, mechanical, and chemical properties. Within the oxide layer, the alloying elements influence the atomic transport such that the alloying focus determines the corrosive habits, with high alloying concentrations (above ∼0.6%) offering protection in opposition to oxide development.